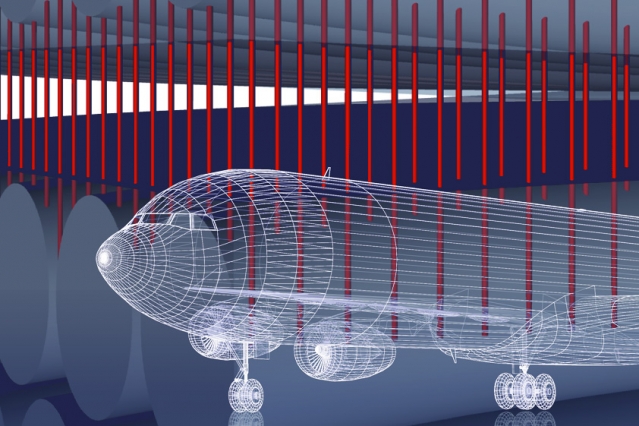
A team of aerospace engineers from MIT determined that carbon nanotube “stitches” make stronger, lighter composites and that this method of reinforcement could help make airplane frames lighter and more damage-resistant.
Today, the newer Airbus and Boeing passenger jets today are made primarily from advanced composite materials such as carbon fiber reinforced plastic, materials that are extremely light and durable that reduce the overall weight of the plane by as much as 20% compared to aluminum-bodied planes. These lightweight air frames result in fuel savings, too.
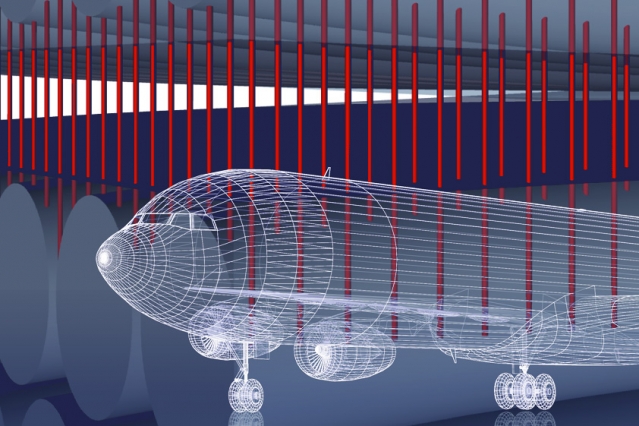
Composite materials happen to have drawbacks though. While aluminum can withstand large impacts before cracking, the many layers in composites can break apart due to relatively small impacts.
Now MIT aerospace engineers have discovered a way to bond composite layers so that the resulting material is much stronger and more resistant to damage than other advanced composites.
The method involves fastening the layers of composite materials together using carbon nanotubes, atom-thin rolls of carbon that are incredibly strong, despite their small size and structure. The team embedded tiny “forests” of carbon nanotubes within a glue-like polymer matrix, then pressed the matrix between layers of carbon fiber composites. The nanotubes, resembled tiny stitches and worked themselves within the crevices of each composite layer, acting as a scaffold to hold the layers together.
In strength tests, the team found that, compared with existing composite materials, the stitched composites were 30% stronger and could withstand greater forces before breaking apart.
According to Roberto Guzman, who led the work as an MIT postdoc in the Department of Aeronautics and Astronautics (AeroAstro), the improvement may lead to stronger, lighter airplane parts like those that require nails or bolts, which can crack conventional composites.
“More work needs to be done, but we are really positive that this will lead to stronger, lighter planes,” said Guzman, who is now a researcher at the IMDEA Materials Institute, in Spain. “That means a lot of fuel saved, which is great for the environment and for our pockets.”
Comments are closed, but trackbacks and pingbacks are open.