3D Printing Metal In Midair Advances Customized Electronics
Typically we think of electronic devices as structured and rigid — and they have been — until recently. The latest trend in electronics is the need for flexible sensors, antennas, and biomedical devices, as well as the growing popularity of wearable electronics.
With this growing trend, researchers have needed to come up with innovative new ways of creating electronics.
Now, a team at Harvard’s John A. Paulson School of Engineering and Applied Sciences (SEAS) and Wyss Institute for Biologically Inspired Engineering have come up with a new way of printing complex metallic architectures, in a way that makes them look like they are suspended in midair.
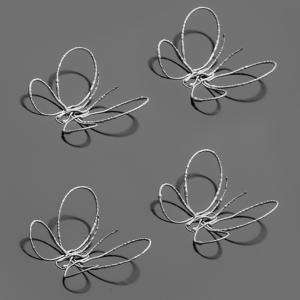
The new method recruits the help of a laser that allows for direct ink writing to create microscopic metallic, free-standing 3D structures that can be created in one step without auxiliary support material.
“I am truly excited by this latest advance from our lab, which allows one to 3D print and anneal flexible metal electrodes and complex architectures ‘on-the-fly,’ ” said Jennifer Lewis, the Hansjörg Wyss Professor of Biologically Inspired Engineering at SEAS and Wyss Core Faculty member.
How they did it
The Harvard team used an ink that was composed of silver nanoparticles and sent it through a printing nozzle. The researchers then heated it and allowed it to cool slowly in order to remove internal stresses and toughen it.
The printing nozzle moves along x, y, and z axes and is combined with a rotary print stage to enable which helps to create the free-form shapes, such as spiral motifs or a butterfly made of silver wires that is less than the width of a hair. As an added bonus, these structures can be printed in free space in just seconds.
The printed wires also act as excellent conductors of electricity, matching the conductivity levels of bulk silver.
The Harvard researchers showed that, in comparison to traditional metal 3D printing techniques, laser-assisted direct ink writing was more efficient when it came to creating curved and complex wire patterns in one step. In addition, localized laser heating allows for the production of electrically conductive silver wires printed directly onto low-cost plastic substrates.
One of the main challenges the researchers had to overcome was creating the ideal distance between the nozzle and the laser.
According to the study’s first author, , the most challenging aspect of honing the technique was optimizing the nozzle-to-laser separation distance.
“If the laser gets too close to the nozzle during printing, heat is conducted upstream which clogs the nozzle with solidified ink,” said Mark Skylar-Scott, Ph.D.,Wyss Institute Postdoctoral Fellow. “To address this, we devised a heat transfer model to account for temperature distribution along a given silver wire pattern, allowing us to modulate the printing speed and distance between the nozzle and laser to elegantly control the laser annealing process ‘on the fly.’ ”
For now, their method is capable of producing a variety of designs like curves, spirals, and sharp angles.
The new ability to write in the air with silver inks can be used in a variety of applications in the production of electronic an medical devices that employ metallic compositions.
Story and video via Harvard University.
Comments are closed, but trackbacks and pingbacks are open.