New 3D printing process creates electronics out of modeling clay
A new method of 3D printing created by Computer Science Professors Michael Jones and Kevin Seppi removes the
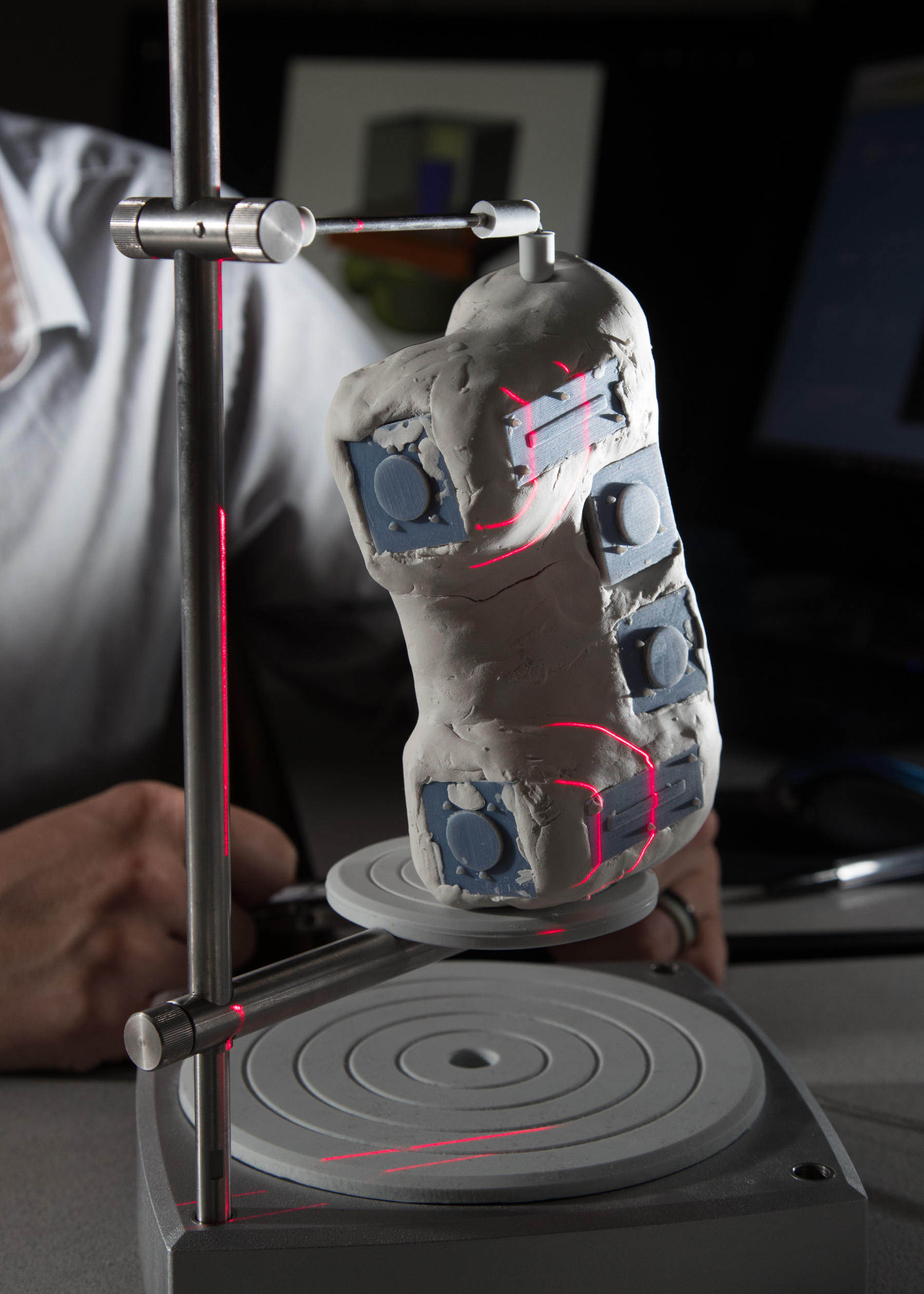
The new technique uses modeling clay to create the basic shape of the desired object around blocks that represent the interactive buttons, knobs, or sliders that will make the object functional.
The complete clay model is then scanned and the computer recognizes each empty space as a certain type of button, so that a real button can be installed once the object is printed.
“Working in clay is awesome until you have to add all the circuitry in it,” said Jones. “With this method, you can get the shape right by working with the clay. Even for people who are skilled in 3D modeling or even if you have years of experience designing models on a computer screen, making a shape that matches an opening in a specific context is pretty tough.” said Michael Jones, Computer Science Professor at the university.
Not only does the computer create the correct shape of the object, but it also determined the best way to halve the object and put all of the circuitry inside.
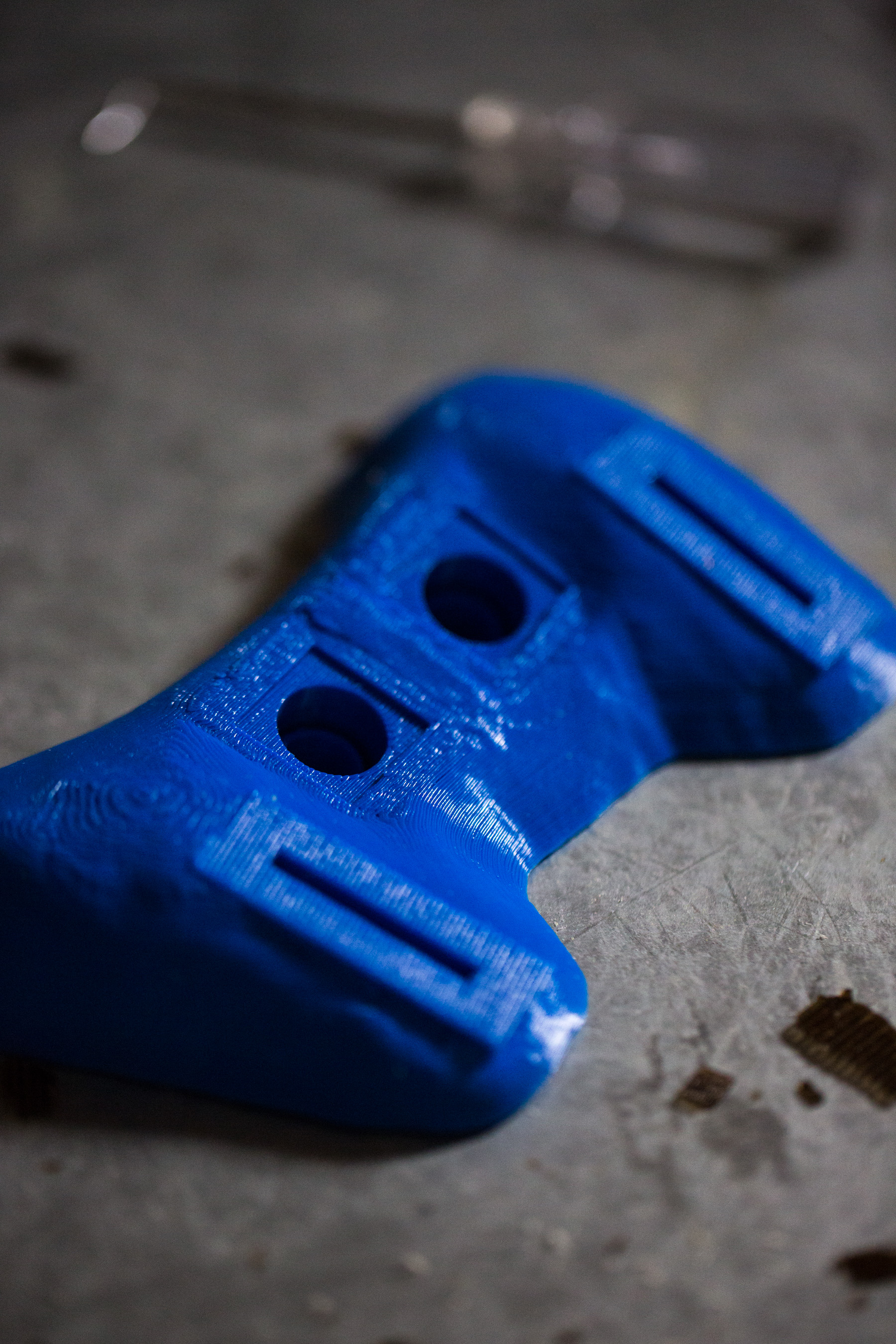
During testing, the researchers showed that it only takes about 30 minutes to sculpt an interactive prototype. Once scanned, it only takes a single button click to finish the 3D modeling process.
The idea of incorporating placeholders into the 3D-printing process emerged last year in the form of stickers to represent where a button would be placed in an object, but the team found it difficult to get the appropriate depth for the button in the printed model.
The algorithm that the team used to identify the blanks in the in clay model also has future applications in motion sensors for functionality.
“We want to develop a circuit that not only senses acceleration and rotation, but also can make sense of that motion,” said Jones. “Whether it’s a sensor in a shoe or a cane, we hope to be able to write programs that interactively learn how to recognize a step or a cane drop accurately.”
Comments are closed, but trackbacks and pingbacks are open.