The Truth About Incorporating Additive Manufacturing Into Your Company’s Production Processes
3D printing is disruptive. Not in a DIY-desktop-kind-of-way, but in a way that arms it with the power to transform production processes so that businesses can reap tangible benefits of its incorporation.
Why, then, are some businesses not even at the point of considering leveraging the technology?
For starters, high costs and complexities of end-product inspection and quality control play a role, but there’s more. Technical skills and lack of global continuity pose challenges. Businesses that should be using the technology haven’t even begun to wrap their heads around how to start.
That’s not to say that it isn’t happening in droves—a transformation right before our eyes.
Companies like BMW, for example, are leveraging 3D expertise to print end-use parts for jugs and fixtures, SpaceX is investing heavily in Metal Additive Manufacturing production, and at GE’s Additive Technology Center in West Chester, OH, 90 3D printers were put to work by 300 designers, machinists, and engineers to create the first-ever FAA certified additive parts.
The transformation is now.
But still, the hurdles exist. Among these is a very real challenge that must be overcome for any business to successfully implement the technology.
According to Kevin Askew, Business Development Manager at GoPrint3D, a company that helps businesses implement additive manufacturing solutions, one of the major barriers to entry is lack of CAD skills. A lot of smaller companies do not have the on-board skills such as familiarity with design programs like Solidworks or Autodesk to even begin. In some cases, says Askew, even larger firms don’t have these capabilities.
In that case, there are companies willing to expand their talent pool. Askew would recommend they even work initially with a third-party CAD designer or a University that would provide students with real-life case studies, which would be mutually beneficial for the company to get what it needs done.
Another challenge companies must face is moving away from doing things a certain way because “that’s the way it’s always been done.”
Let’s take materials, for example. A company like GoPrint3D provides access to over 85 materials, everything from entry grid plastics to metal, powders, and flight-certified plastics, but when Askew asks clients why they’re using a certain material, sometimes the response is one of legacy and not necessarily the best or least expensive option. Once you open the door to material varieties, the next hurdle to overcome is the limitations of the equipment.
“Materials are less of a challenge, it’s more budget of the machine that can use that material,” says Askew. In order to print in higher grade polymers, for example, certain machine factors must be in place.
So, are businesses really tapping into the power of 3D printing? Yes and no. According to Askew, there are still those roadblocks to overcome, including lack of technical talent, but it’s possible and well-worth it.
Chris Walling, Sr. Manager, Supply Chain Solutions, IndustryStar Solutions, echoes this point. Walling is helping companies create more productive and efficient supply chains by implementing the technology.
“By using additive manufacturing technology, companies are now able to reduce upfront capital expenses, take their products to market faster, and significantly reduce launch risk through high-quality additive manufacturing,” says Walling.
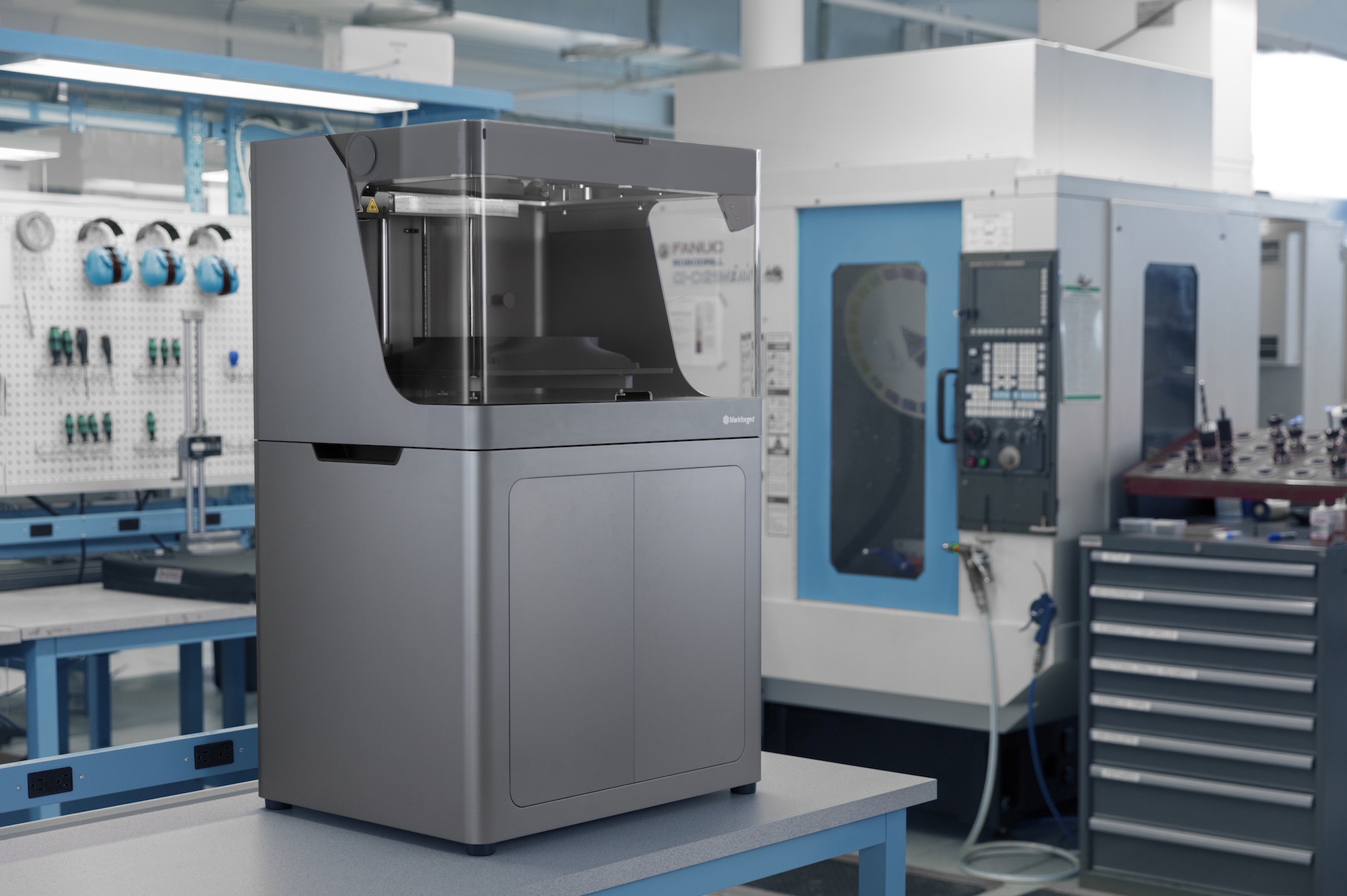
These are the real reasons businesses finally come to terms with the disruptive technology and take the steps necessary to implement:
Cost-Savings
If companies are expecting to notice the cost-saving effects of 3D printing immediately, they’re not fully aware of how the technology works. It can cut some costs, for example, at the launch phase of products, by creating prototypes of first-runs without expensive tools, products or components, but the real cost-savings will be seen down the road. This is an investment.
“Whether that’s a direct cost from part to part, often that doesn’t work as a linear comparison, but once you take into account the ripple effect of the 3D printed parts: cost savings, time to market, keeping intellectual property in house, if you’re looking at short production runs (lows hundreds or thousands), it can cut material costs,” says Askew.
Reduce Production Times
Traditional manufacturing processes can extend launch timelines.
“By taking advantage of additive manufacturing techniques, a company can take a new product to market in a fraction of the time, compared to the time it takes to procure traditional tooling, perform the necessary quality tests, and produce the first units,” says Walling.
Companies like BPM Microsystems exhibit the essence of decreased production time. The company’s engineering and production teams experimented with 3D printing individual site chassis. They were able to rapidly iterate different prototypes (and by rapidly, we mean overnight, compared to ordinary five to eight-week turnaround times). The final pieces were printed in carbon fiber filament and the new process allowed for an existing platform to increase capacity by 75% while reducing material costs to just over $10. Site chassis no longer need to be ordered in advance or pulled from existing inventory. Now they can be printed on-demand when the order comes in.
The reality is, as Askew points out, additive manufacturing can eliminate a lot of the reliance on supply chain processes. And that’s appealing to companies.
Weight Benefits
Lighter components are a major reward for engineers. When you can reduce the weight of your components and reduce the number of components needed by merging them into one or five (down from over 50), the benefits expand even more.
Lowers New Product Launch Risk
“Many companies that hit stumbling blocks early during their new product launches didn’t have the foresight to develop a supply chain structure and processes flexible enough to allow them to quickly pivot as they receive marketplace feedback, or to pilot ideas on small scale before a large-scale launch,” says Walling.
By implementing additive manufacturing into the process, companies can easily adjust instead of making costly revisions.
It All Comes Down to Money
New technologies such as machine learning and multi-materials printing are expanding additive manufacturing even further for businesses. Now it’s a matter of recruiting the right team, embracing the benefits, and acting.
“At the end of the day, it all does center around cost,” says Askew.
Companies that embrace, are bound to reap the financial benefits, if done correctly. Although not always immediate, nothing quickly earned was ever long-lasting, so additive manufacturing’s long-term benefits are still unfolding.