This Robotic Finger Looks, Feels, And Acts Just Like The Real Thing
Over the past few years there has been an influx of bio-inspired robots ranging from robots with reptile tails, ones with fish characteristics, and even some with insect qualities.
Now researchers from Florida Atlantic University have developed a bio-inspired robot that mimics the human finger — and it looks pretty realistic.
When we think of robots, we think of hard, rigid parts that don’t have much range of motion, but a scientist from Florida Atlantic University has developed and tested a lifelike robotic finger using shape memory alloy (SMA), a 3D CAD model of a human finger, a 3D printer, and a unique thermal training technique.
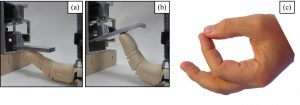
“We have been able to thermomechanically train our robotic finger to mimic the motions of a human finger like flexion and extension,” said Erik Engeberg, Ph.D., assistant professor in the Department of Ocean and Mechanical Engineering within the College of Engineering and Computer Science at FAU. “Because of its light weight, dexterity and strength, our robotic design offers tremendous advantages over traditional mechanisms, and could ultimately be adapted for use as a prosthetic device, such as on a prosthetic hand.”
The team used a 3D CAD model of a human finger in order to create a solid model and then 3D printed the inner and outer molds that enclosed a flexor and extensor actuator and position sensor. The extensor actuator takes a straight shape when it’s heated and the flexor actuator takes a curved shape when heated. To put the whole finger together, they used SMA plates and a multi-stage casting process. They also designed an electrical chassis to allow electric currents to flow through each SMA actuator. Their U-shaped design directed the electric current to flow the SMAs to an electric power source at the base of the finger.
How it works
This new technology employed heating and cooling to operate the robotic finger. When the actuator cooled, the material relaxed slightly.
“Because SMAs require a heating process and cooling process, there are challenges with this technology such as the lengthy amount of time it takes for them to cool and return to their natural shape, even with forced air convection,” said Engeberg. “To overcome this challenge, we explored the idea of using this technology for underwater robotics, because it would naturally provide a rapidly cooling environment.”
The team has developed the finger for use in undersea operations in order to address some of the difficulties and challenges humans encounter while working in the ocean depths, so it includes thermal insulators on the fingertip which are kept open for water to flow inside of the finger. When the finger flexes and extends, water flows through each insulator and cools the actuators.
“Because our robotic finger consistently recovered its thermomechanically trained shape better than other similar technologies, our underwater experiments clearly demonstrated that the water cooling component greatly increased the operational speed of the finger,” said Engeberg.
Watch a demo from FAU’s BioRobotics Lab below.
For more information visit Florida Atlantic University.