Unprecedented Fusion of Power and Finesse Seen in Robotic Grippers
Researchers at North Carolina State University have developed a robotic gripping device. In addition to possible manufacturing applications, the researchers also integrated the device with technology that allows the gripper to be controlled by the electrical signals produced by muscles in the forearm, demonstrating its potential for use with robotic prosthetics.
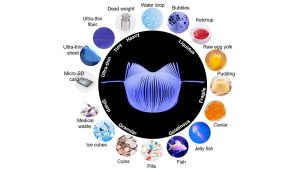
The design for the new grippers builds on an earlier generation of flexible, robotic grippers that drew on the art of kirigami, which involves cutting and folding two-dimensional sheets of material to form three-dimensional shapes.
“Our new grippers also use kirigami but are substantially different, as we learned a great deal from the previous design,” says Yaoye Hong, co-author of the paper and a recent Ph.D. graduate from NC State. “We’ve been able to improve the fundamental structure itself, as well as the trajectory of the grippers – meaning the path at which the grippers approach an object when grabbing it.”
“The strength of robotic grippers is generally measured in payload-to-weight ratio,” Yin says. “Our grippers weigh 0.4 grams and can lift to 6.4 kilograms. That’s a payload-to-weight ratio of about 16,000. That is 2.5 times higher than the previous record for payload-to-weight ratio, which was 6,400. Combined with its characteristics of gentleness and precision, the strength of the grippers suggests a wide variety of applications.”
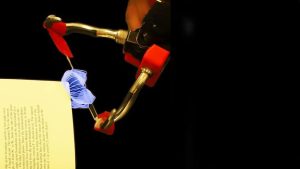
The new design can achieve high degrees of strength and gentleness because it distributes force throughout the structure of the gripper. The researchers also integrated the gripping device with a myoelectric prosthetic hand, meaning the prosthesis can be controlled using muscle activity.
“This gripper provided an enhanced function for tasks that are difficult to perform using existing prosthetic devices, such as zipping certain types of zippers, picking up a coin, and so on,” says Helen Huang, co-author of the paper and Jackson Family Distinguished Professor in the Joint Department of Biomedical Engineering at NC State and the University of North Carolina at Chapel Hill.
“The new gripper can’t replace all of the functions of existing prosthetic hands, but it could be used to supplement those other functions,” Huang says. “One of the advantages of the Kirigami grippers is that you would not need to replace or augment the existing motors used in robotic prosthetics. You could use the existing motor when utilizing the grippers.”
In proof-of-concept testing, the researchers demonstrated that the kirigami grippers could be used with the myoelectric prosthesis to turn the pages of a book and pluck grapes off a vine.
“We think the gripper design has potential applications in fields ranging from robotic prosthetics and food processing to pharmaceutical and electronics manufacturing,” Yin says. “We are looking forward to working with industry partners to find ways to put the technology to use.”