A chip designed just for you? Why an Application Specific Integrated Circuit (ASIC) can give your product the edge
While it may not be common knowledge, ASICs have transformed many electronics products. Even a mid-range vehicle manufactured some years ago will feature several specialized ASICs for tire pressure monitoring, engine monitoring, and gas sensors. ASICs are also establishing their place in many industrial applications, but despite their benefits, there’s still a misconception that the technology is unattainable for many manufacturers. Fortunately, the path to commissioning an ASIC is not singular, as Richard Mount, Director of Sales at Swindon Silicon Systems, explains.
If you were to sit in the driver’s seat of your car and glance at the features available at your fingertips, you’d be looking at a surprisingly large number of ASIC-driven technologies. These are often mixed-signal devices that combine the benefits of analog and digital technologies in a single chip and are found in every system, from climate control and airbag deployment to infotainment systems and tire pressure sensing.
Continuous development in ASIC design has also driven many other industrial sectors to choose custom integrated circuits (ICs) as a cost-effective alternative to traditional off-the-shelf components. ASICs are used wherever capability, size, cost, and, in many cases, resistance to somewhat complex environments are essential design requirements.
However, despite their growing prevalence across the industry, there’s still a mistaken belief that the non-recurring engineering (NRE) costs and time implications of commissioning an ASIC make them unfeasible. Therefore, the onus is on ASIC designers and suppliers to bust those myths and suggest methods that can help ASICs fit within a manufacturer’s budget.
Why choose an ASIC?
First, look at why a manufacturer should choose a custom ASIC. With many existing applications, it can often be beneficial to port a current design into an ASIC to introduce new functionality and performance in a much smaller form factor while allowing backward compatibility. In such an instance, an ASIC comes into its own if a manufacturer’s existing component supplier is making a process obsolete, but the product still has decades of potential. It is possible to re-engineer a drop-in replacement to continue the product’s availability.
However, there are many instances where it’s prudent, both technically and commercially, to develop an ASIC during the initial product design. As part of the process, the engineering team provides a specification that outlines their functionality and performance criteria, and the ASIC supplier wholly designs and produces the custom IC solution.
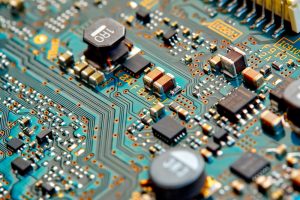
One of the principal reasons why a company will commission an ASIC is to protect its intellectual property (IP). Typically, a printed circuit board (PCB) comprises various mounted discrete components, including commercial off-the-shelf (COTS) ICs. However, anybody skilled in electronics design can reverse engineer the PCB and replicate the product. The strength of an ASIC is that it is tough to reverse engineer the IC or for it to be “reused” when compared to a board-level design, thus ensuring that the IP is for the owner’s benefit and theirs alone.
From an engineer’s viewpoint, the real excitement comes from the clean slate approach that ASICs offer. For the most part, the standard requirement for an ASIC is to provide enhanced and optimized performance in a minimal footprint with low power consumption.
We can return to the automotive tire pressure monitoring system example to see how this works in the real world. Here, the system-in-package (SiP) sensor includes an ASIC capable of seeing deficient voltage levels from a co-packaged MEMS sensor and provides signal conditioning and processing along with RF data transmission to the vehicle. Each sensor is calibrated over temperature and pressure to ensure high degrees of measurement accuracy. Its power is supplied by a lithium button battery, where operational life has to be guaranteed for many years, so shallow power methods are used extensively.
This starkly contrasts with a typical discrete design’s performance, where it would not be possible to achieve the same measurement accuracy and performance in the same footprint with the required battery life.
No need to start from scratch
If a manufacturer wants an ASIC, they may still assume they need more budget or time to realize their ambitions. The truth is, however, that ASIC developers have many ways to make an ASIC solution accessible to a variety of applications and markets.
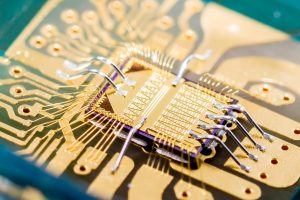
To ensure minimal budgets and time, it’s possible to reuse existing IP in new or existing projects, shortcutting much of the design and verification. An established ASIC company should have access to many acquired circuit block IPs. Still, designers can license IP blocks from specialist vendors or use foundry IP when in-house IP is unavailable.
IP obtained in either way can often be tweaked in-house, allowing it to meet customer-specific requirements. This flexibility means highly complex systems can be monolithically integrated in far shorter timescales than starting from scratch.
Thanks to developments in ASIC design and manufacture, many companies are considering and embarking on developing their device customized to their product requirements. Choosing a trustworthy, qualified ASIC partner will be the key to success — one that can deliver both the design and production test of the ASIC, using only in-house capabilities, is a prudent first step.
Provided by Swindon Silicon Systems